How the Advanced Ozone Cleaning Process Improves Wafer Yields and Reduces Costs
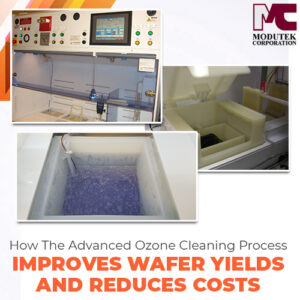
Editor’s Note: This article was originally published in January 2017 and has been updated with additional information and reposted in April 2023. Modutek’s advanced ozone cleaning is a highly effective method for removing contaminants from wafers. The process involves using ozone gas, which is a highly reactive oxidant, to break down and remove organic and […]
Why Megasonic Cleaning is Essential for Silicon Wafer Processing
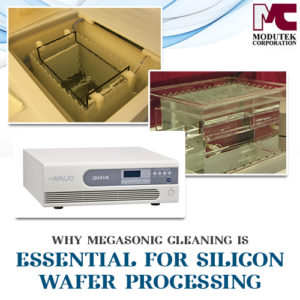
Adding Megasonic cleaning to standard wafer cleaning methods can reduce costs and improve overall semiconductor fabrication performance. Megasonic cleaning is especially useful for manufacturing silicon wafers with the smallest geometries, where almost complete particle removal is necessary for successful manufacturing. The process uses high-frequency sound waves to clean wafer surfaces and can be integrated into […]