Silicon Wafer Etching Processes for Wet Processing Applications
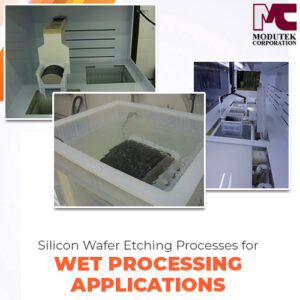
Editor’s Note: This article was originally published in September 2016 and has been updated with additional information and reposted in June 2023. The production of semiconductor components relies on the etching of silicon wafers using various processes like KOH etching to create the necessary structures and connections. To meet etching requirements, Modutek offers cutting-edge wet […]
Why Pre-Diffusion Cleans Are Essential for Silicon Wafer Processing
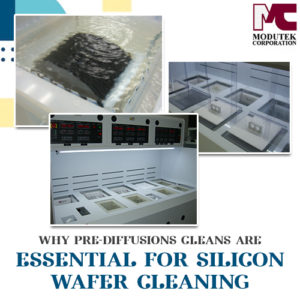
Silicon wafers must be completely clean before they go through the diffusion process. If contaminating particles are present on the wafer surfaces during the diffusion process, they will cause defects in the final semiconductor product. Pre-diffusion cleaning can be carried out with several methods. RCA clean and Piranha etch use chemicals to strip away wafer […]
How Specialized Equipment Improves Silicon Wet Etching Processes
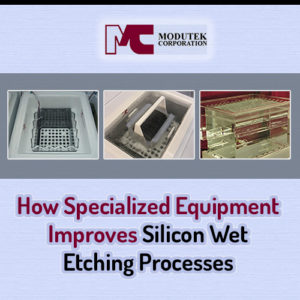
Results from common wet etching processes such as KOH and Piranha etch can be improved with the use of specialized equipment. Depending on the process, key parameters can be controlled especially well and innovative procedures can reduce particle counts. When specialized equipment is used in silicon wet etching processes, wafer output can increase, defects can […]