Safety Protocols for Using Wet Bench Equipment
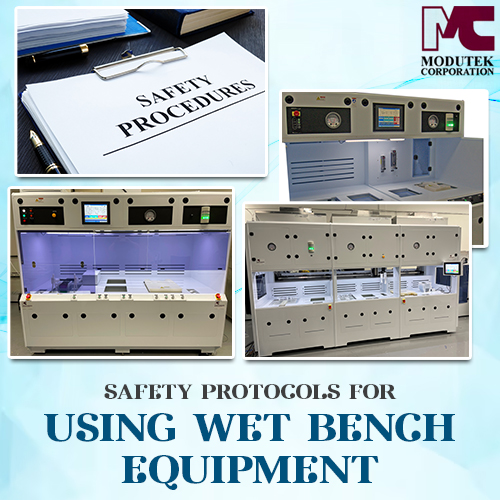
In semiconductor manufacturing and research lab environments, the importance of safety cannot be overstated. These environments, known for their intricate processes and delicate handling of materials, necessitate stringent safety protocols to protect both personnel and products. This is particularly crucial when dealing with wet bench equipment, a central component in the semiconductor industry for various […]
How to Develop a Requirements List When Buying Wet Bench Equipment
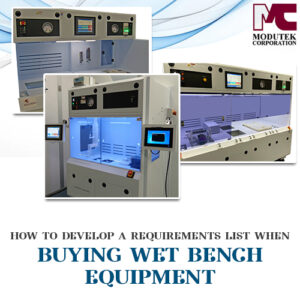
Editor’s Note: This article was originally published in March 2015 and has been updated with new information and reposted in August 2023. Wet bench equipment is an integral component that semiconductor manufacturing and research industries need. From cleaning, etching, stripping, developing, and testing new processes, it plays a vital role in these fields. The range […]