5 Things About Wet Benches You Should Know
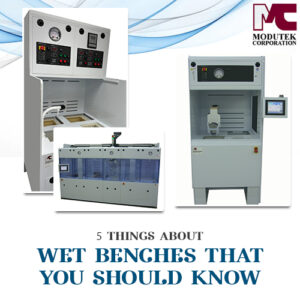
Editor’s Note: This article was originally published in February 2015 and has been updated with new information and reposted in October 2023. When you choose a reputable supplier of wet benches, your process can be efficient, flexible, and safe. Ideally, the supplier will be a manufacturer of wet bench equipment, performing most of the design, […]
Using RCA Clean in a Wet Bench Process
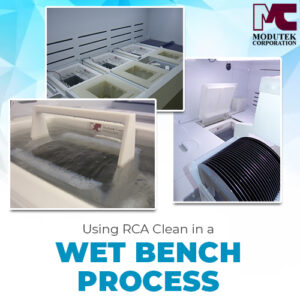
Editor’s Note: This article was originally published in May 2015 and has been updated with new information and re-posted in August 2023. The semiconductor manufacturing industry relies heavily on complex and precise processes to create electronic components we rely on every day. One such process is wafer cleaning – an essential step that removes unwanted […]
Selecting a Wet Bench Manufacturer That Meets Your Process Requirements
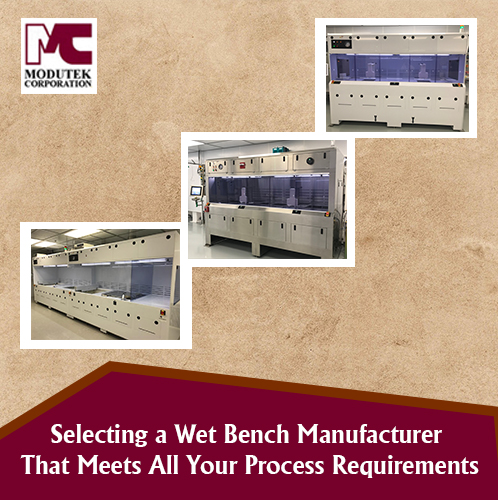
Semiconductor device fabrication can be a complex process. Often, it can take as many as eight weeks to complete a manufacturing cycle. During this process it’s critical to use wet bench stations that are built with high quality components that work reliably. This is needed to ensure that every manufacturing process involved complies with important […]
Modutek at 2019 Semicon Conference in China-Hall N3 Booth 3243
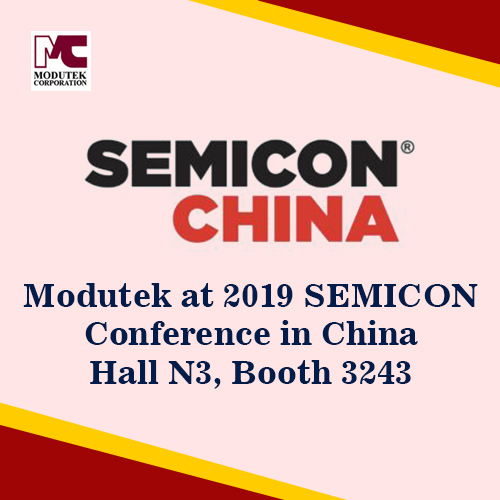
Modutek Corporation, a leading supplier of wet bench stations and wet process equipment, will be at the Semicon Conference located at the Shanghai International Expo Center in China from March 20-22, 2019. At the Conference Modutek and their factory representative Laserwort Ltd., will be located in Hall N3 at booth 3243. Additional details about the […]
Why Chemical Lift Station Pumps Are Needed for Wet Bench Stations
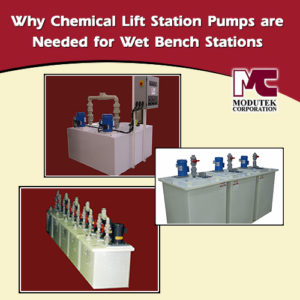
Once a wet bench process step is completed, the remaining chemicals and waste water have to be drained and transferred to an area for neutralization and disposal. Depending on the physical layout of the semiconductor manufacturing facility, gravity draining may either not be possible at all or may be insufficient in terms of flow and […]
How to Safely Use Solvents for Wafer Processing
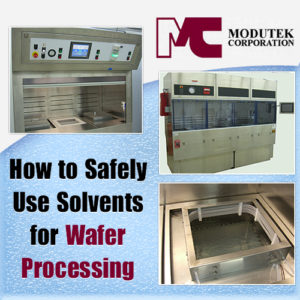
At semiconductor research centers and foundries, solvent wet bench stations provide a critical role in the semiconductor fabrication process. These stations are designed for operations that include substrate cleaning, photoresist stripping and liftoff pattern transfers. Since the solvents are often highly inflammable, wet bench equipment needs to be designed with stringent compliance to safety codes. Equipping […]
How Wet Bench Stations Are Tailored for Specific Manufacturing Process Requirements
The fabrication of semiconductor wafers requires that an elaborate set of chemical etching, stripping and cleaning steps be followed in a precise procedure that can be consistently repeated. The semiconductor manufacturing process requires that the use of hydrofluoric acid and other chemicals which must precisely controlled and monitored. These high-tech processes are critically important to […]
Designing Semiconductor Manufacturing Equipment for Ergonomics and Safety
Semiconductor manufacturing processes routinely use chemicals and procedures that could result in accidents if the manufacturer did not have a serious commitment to safety. Safety guidelines such as SEMI S2, published by the global industry association for microelectronics manufacturers, help manufacturers implement safe operating protocols. Ergonomic designs for semiconductor manufacturing equipment as described in SEMI S8 […]