How Megasonic Cleaning Improves Silicon Wafer Manufacturing
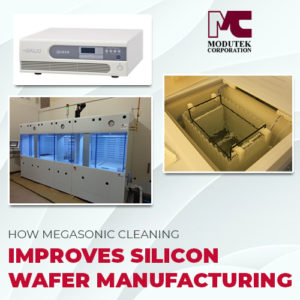
When silicon wafers are cleaned between manufacturing steps, it is critical to remove all contamination from the wafer surfaces. The remaining traces of process chemicals or microscopic particles can disrupt the etching process and result in defective or low-quality semiconductor devices. Megasonic cleaning uses high-frequency sound waves in the cleaning tank to remove contaminants and […]