5 Things About Wet Benches You Should Know
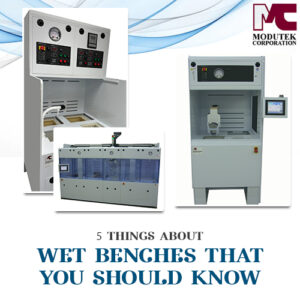
Editor’s Note: This article was originally published in February 2015 and has been updated with new information and reposted in October 2023. When you choose a reputable supplier of wet benches, your process can be efficient, flexible, and safe. Ideally, the supplier will be a manufacturer of wet bench equipment, performing most of the design, […]
5 Important Things to Know When Buying Wet Bench Stations
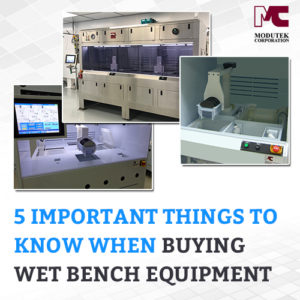
Because semiconductor manufacturing relies on a large number of process steps and complicated sequencing, wet benches need to be tailored to meet requirements for a specific application. Before focusing on the process-specific requirements, there are general questions that should be answered. This helps narrow down the selection criteria before making the purchasing decision. General questions […]
Why Chemical Lift Station Pumps Are Needed for Wet Bench Stations
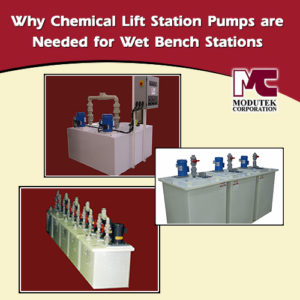
Once a wet bench process step is completed, the remaining chemicals and waste water have to be drained and transferred to an area for neutralization and disposal. Depending on the physical layout of the semiconductor manufacturing facility, gravity draining may either not be possible at all or may be insufficient in terms of flow and […]
How Wet Bench Stations Are Tailored for Specific Manufacturing Process Requirements
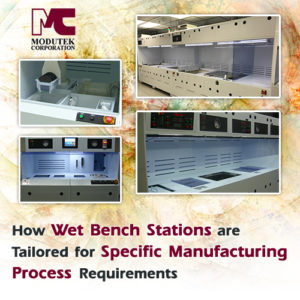
The fabrication of semiconductor wafers requires that an elaborate set of chemical etching, stripping and cleaning steps be followed in a precise procedure that can be consistently repeated. The semiconductor manufacturing process requires that the use of hydrofluoric acid and other chemicals which must precisely controlled and monitored. These high-tech processes are critically important to […]
Designing Semiconductor Manufacturing Equipment for Ergonomics and Safety
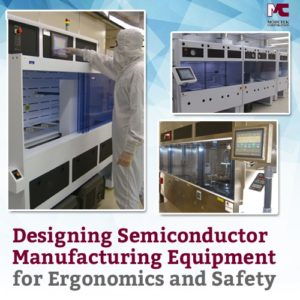
Semiconductor manufacturing processes routinely use chemicals and procedures that could result in accidents if the manufacturer did not have a serious commitment to safety. Safety guidelines such as SEMI S2, published by the global industry association for microelectronics manufacturers, help manufacturers implement safe operating protocols. Ergonomic designs for semiconductor manufacturing equipment as described in SEMI S8 […]